- Author: Virgil
The RF laser tube (Radio Frequency laser source) enables precise frequency modulation, allowing users to directly adjust the laser’s pulse frequency within LightBurn software. This functionality provides granular control over pulse characteristics, optimizing energy distribution, thermal effects, and material interaction during engraving. By modulating the frequency, operators can fine-tune engraving outcomes, minimizing heat-affected zones and achieving greater precision across various substrates.
This article outlines the process for modifying RF laser tube frequency to enhance engraving accuracy and material adaptability. Let’s dive in now!
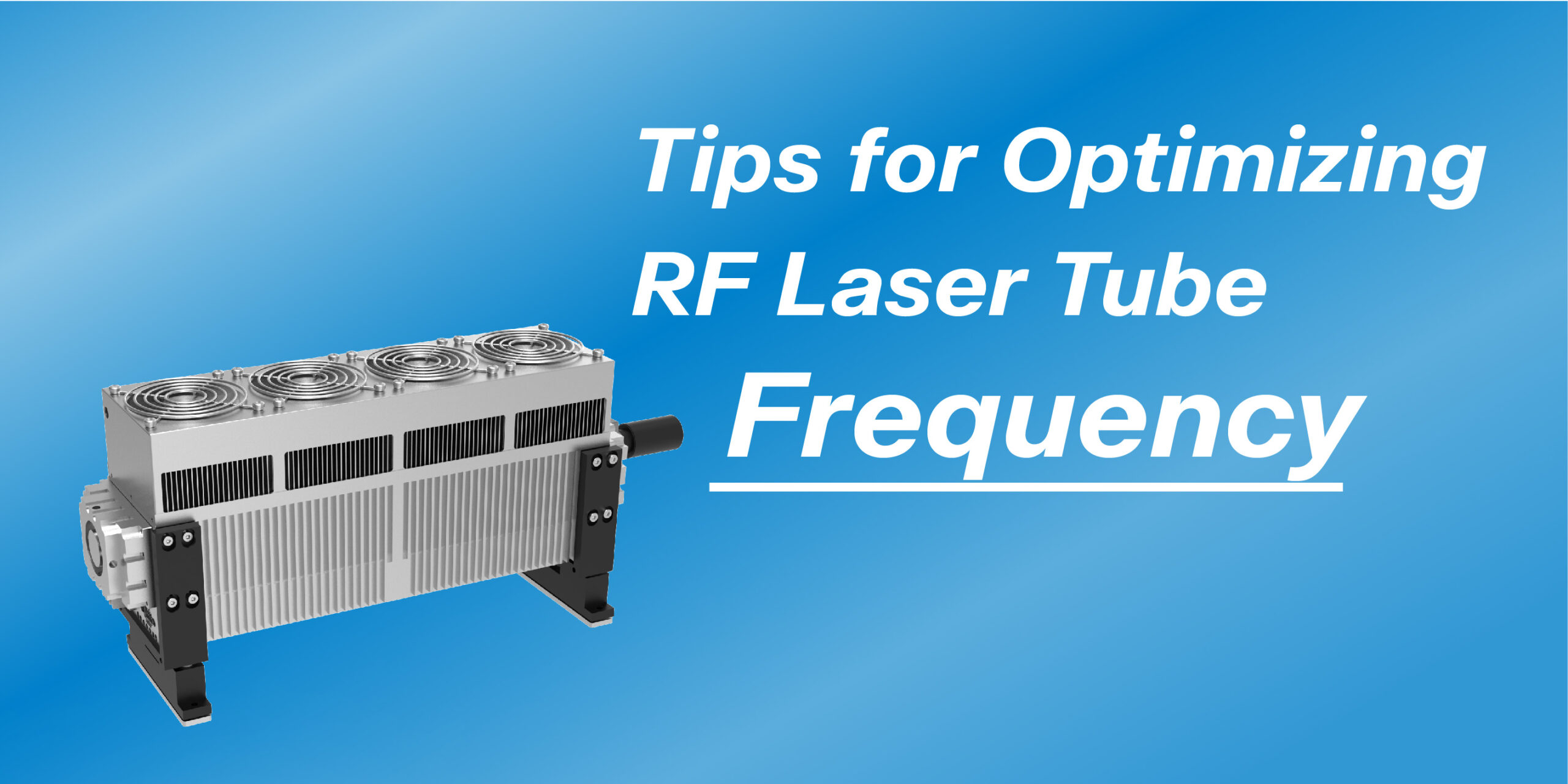
1. What is RF Laser Tube Frequency?
RF laser tube frequency refers to the rate at which laser pulses are emitted per second, measured in Hertz (Hz). Unlike continuous-wave lasers, RF lasers function by rapidly turning on and off, with the frequency determining the speed and intensity of these pulses.
Lower frequencies result in fewer but more powerful pulses, making them ideal for deep cutting or material processing that requires high energy concentration.
Conversely, higher frequencies generate a greater number of pulses with lower energy per pulse, which is better suited for fine engraving and reducing heat-affected zones on delicate materials.
Selecting the appropriate frequency ensures optimal precision and efficiency in both engraving and cutting applications.
2. Why Optimizing RF Laser Tube Frequency Matters
Properly optimizing RF laser tube frequency enhances engraving and cutting precision, extends machine longevity, and improves efficiency. Fine-tuning frequency settings ensures that each material is processed with the best balance of speed, power, and energy distribution. Below are key reasons why frequency optimization is crucial:
Improved Cutting and Engraving Quality
Selecting the correct frequency can minimize defects such as excessive charring, rough edges, or incomplete cutting. Low-frequency provide deep cuts with stronger penetration. However, high-frequency one enable fine and intricate engraving with reduced surface damage. With fine-tuned parameters, you can achieve a precise and high-contrast engraving and clean cutting.
Material-Specific Adjustments
Every material responds differently to laser energy, requiring customized frequency settings to optimize results. For example, wood benefits from lower frequencies to ensure deeper cuts without excessive burning, while acrylic requires higher frequencies for smooth, polished edges. Proper frequency selection prevents material damage and enhances overall engraving or cutting quality.
Thermal Management
Frequency adjustments directly impact heat generation and dissipation during laser processing. Lower frequencies concentrate more heat per pulse, which is useful for cutting but can cause overheating or scorching if not properly controlled. Higher frequencies spread the heat more evenly, reducing the risk of warping, discoloration, or material distortion. Balancing frequency with power and speed settings helps maintain temperature control for optimal performance.
Extended Laser Tube Lifespan
Operating the RF laser at an optimal frequency range reduces wear and extends the working life of the tube. Running the laser at improper frequency settings—whether too low or too high—can lead to inefficient energy use and premature degradation of components. Proper frequency optimization ensures the system operates smoothly with minimal mechanical and thermal stress.
Production Efficiency
Efficient frequency settings allow for faster engraving and cutting speeds without compromising quality. High-frequency settings improve workflow efficiency by enabling smooth, rapid engraving for intricate designs, while lower frequencies enhance cutting performance for thicker materials. By fine-tuning frequency settings in conjunction with power and speed adjustments, operators can achieve superior results while reducing processing time and material waste.
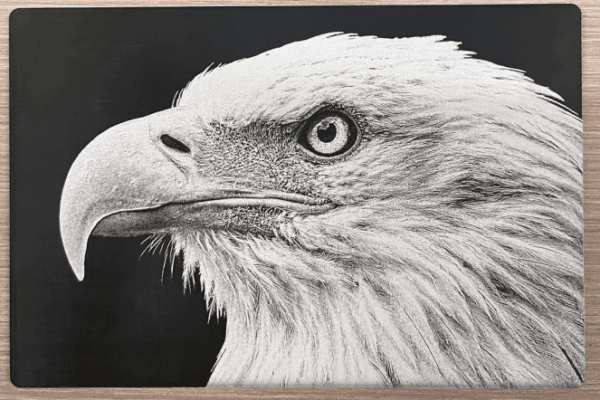
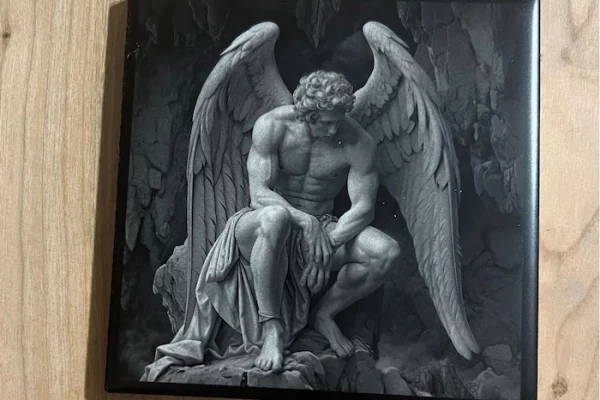
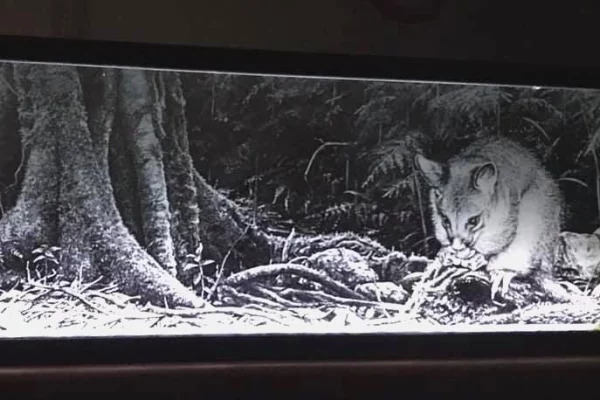
3. Factors That Influence RF Laser Tube Frequency
Several factors play a role in determining the optimal RF laser tube frequency for a given application. Understanding these influences can help operators fine-tune their laser settings for better results.
Material Properties
Different materials absorb and react to laser energy in distinct ways. Softer materials like fabric or rubber may require higher frequencies to minimize scorching, while denser materials like metals or wood may benefit from lower frequencies for deeper cuts.
Application Type
Engraving, cutting, and marking all require different frequency settings. Engraving often benefits from higher frequencies to ensure smooth detailing, whereas cutting may require lower frequencies for stronger penetration.
Power Output
The relationship between power and frequency must be balanced. Higher power with lower frequency enhances depth but can create burn marks, while lower power with high frequency produces detailed but shallow engravings.
Cooling and Heat Dissipation
Effective heat management is critical, as excessive heat buildup can lead to material distortion or damage. Adjusting the frequency alongside airflow or cooling mechanisms can prevent unwanted thermal effects.
Machine Capabilities
The laser machine’s hardware specifications, including the RF tube wattage and beam quality, influence how different frequencies interact with materials. Machines with advanced control systems allow finer adjustments for improved precision.
4. Material Interaction with Frequency Settings
RF laser frequency affects energy delivery, influencing cutting depth and engraving precision. Lower frequencies enable deep cuts, while higher frequencies distribute heat evenly to prevent damage. Choosing the right setting ensures clean results, as well as cutting thick materials or engraving delicate surfaces.
Low Frequency (1-5kHz):
- Longer intervals between rhythms allow materials to cool a little between pulses.
- Suitable for cutting thicker products like hardwood or even leather-made, where deep penetration is needed to have.
Medium Frequency (5-20kHz):
- Briefer intervals between pulses give well balanced energy distribution.
- Ideal for materials like plastics or thin steels that need clean cuts and moderate depth.
High Frequency (20-50kHz or higher):
- Really brief periods between rhythms distribute heat more equally.
- Best for inscribing fragile materials like glass or even acrylic to reduce gaps or even damages.
- Minimizes incinerate results on all natural components like cloth or even newspaper, far better for sparse materials or even precision decreases.
5. Practical Comparisons Between Low and High Frequency
Understanding the practical differences between low and high RF laser frequencies helps in selecting the right settings for specific applications. The primary differences are evident in engraving and cutting results.
5.1. Engraving:
Low Frequency (1-5kHz)
Produces deeper engravings with higher energy per pulse. However, this can lead to rougher surfaces and potential charring, especially on organic materials.
High Frequency (20-50kHz)
Generates shallower but cleaner engravings. The increased pulse rate distributes energy more evenly, resulting in smooth, detailed inscriptions with minimal thermal damage.
5.2. Cutting:
Low Frequency (1-5kHz)
Cuts deeper and is more effective for thick, dense materials like hardwood and leather. The higher energy per pulse ensures strong penetration but may leave rough or slightly charred edges.
High Frequency (20-50kHz)
Produces cleaner, smoother edges with less material distortion. The reduced energy per pulse minimizes burning, making it ideal for precision cutting of thin or heat-sensitive materials like acrylic and textiles.
By considering these comparisons, users can adjust frequency settings to match their specific needs, whether for deep, high-impact engraving or for smooth, detailed precision cutting.
6. Key Considerations in Adjusting Frequency
- a. Material Sensitivity: Softer or even heat-sensitive products (e.g., newspaper, cloths) normally perform far better at greater regularities to lessen burn signs.
- b. Cutting vs. Engraving: Lower regularities are actually commonly a lot better for reducing as they deliver extra power per rhythm.
- c. Engraver Capabilities: Ensure your laser etching equipment can carefully working at the decided on regularity selection.
7. Balancing Frequency with Other Laser Parameters
RF laser frequency does not operate in isolation; it must be balanced with power and speed settings to achieve the desired output.
High Frequency with…
Low Power:
Produces finer details, making it ideal for intricate engravings. However, due to the lower power, the engraving may lack depth and contrast, particularly on harder materials. This setting works best for marking delicate surfaces where precision is a priority.
High Power:
Generates deep, smooth engravings but can lead to excessive heat buildup. This may cause unwanted material distortion, particularly in heat-sensitive materials like acrylic or thin metals. Careful power adjustments are necessary to prevent warping or burns.
Slow Speed:
Results in a deeper, darker engraving due to prolonged exposure. This can be useful for achieving high-contrast engravings, but on some materials, it may produce a burned or carbonized effect, particularly on wood and organic materials.
Fast Speed:
Produces smooth, shallow engravings, making it a great setting for detailed, high-resolution work. The shorter exposure time reduces burn marks and ensures clean results, particularly on acrylic and coated metals.
Low Frequency with…
Low Power:
Produces shallow, spaced-out markings that may appear dotted. Since the laser pulses are less frequent, the engraving may lack uniformity, particularly on hard materials. This setting is best suited for light etching on soft materials.
High Power:
Increases engraving or cutting depth significantly but can lead to excessive burning or charring, especially on wood and other organic materials. While this setting is effective for deep engraving, it requires precise control to avoid overburning.
Slow Speed:
Creates deep, strong engravings with better heat control compared to high-frequency settings. This is ideal for cutting thick materials such as leather and wood, where deeper penetration is needed without excessive heat spread.
Fast Speed:
Produces faint or dotted engravings with visible gaps in the marking. This setting is useful when a subtle marking effect is required but may not be ideal for applications requiring high contrast or clarity.
Summary Table
Frequency | Power | Speed | Effect |
---|---|---|---|
High | Low | - | Fine details but lacks depth |
High | High | - | Deep, smooth engraving but risk of heat buildup |
High | - | Slow | Deep, dark engraving with potential burning |
High | - | Fast | Smooth, shallow engraving, ideal for intricate work |
Low | Low | - | Shallow, spaced markings with visible dots |
Low | High | - | Increased depth but risk of excessive burning |
Low | - | Slow | Deep, strong engraving with less heat spread, ideal for thick materials |
Low | - | Fast | Faint or dotted engraving with gaps in the mark |
Understanding this interplay among different parameters enables precise control over engraving and cutting quality.
Learn more: Parameters Settings to Engrave/Cut Perfect Projects!
8. RF Laser Vs. DC Glass Laser
RF (Radio Frequency) and DC (Direct Current) laser tubes have distinct differences, particularly in precision, durability, and energy efficiency. The following comparison highlights key aspects of both technologies:
Feature | RF Laser Tube | DC Glass Laser Tube |
---|---|---|
Beam Quality | High precision, fine engraving | Lower precision, less refined engraving |
Lifespan | 10,000-20,000 hours | 2,000-5,000 hours |
Engraving Speed | Faster, higher pulse frequency | Slower, continuous wave operation |
Maintenance | Low, sealed system | Higher, requires gas refilling |
Initial Cost | More expensive | More affordable |
Cutting Power | Suitable for thin materials | Better for deep cutting |
Heat Management | Less thermal stress, reduced material damage | Higher heat buildup, risk of burns |
Learn more: RF Laser VS DC Glass Laser
In summary, RF lasers excel in precision applications, offering better engraving quality and longevity, while DC lasers are cost-effective and better suited for cutting applications. Selecting the right laser depends on the specific needs of the project.
9. How to Adjust RF Laser Frequency in LightBurn?
Step #1: Access Machine Settings
- Open up LightBurn as well as hook up to your laser device.
- Get through to “Edit” > “Machine Settings”.
Step #2: Locate Frequency Settings
- Look for the “Laser Control” or “Advanced” tab where the frequency or even PWM (Pulse Width Modulation) setups are configured.
Step #3: Input Frequency Range
- Get into the desired frequency market value within the permitted variety. For Thunder Laser latest RF laser cutter and RF laser engraver, which mainly feature 30W, 55W, and 60W RF laser tube, the recommended frequency would be 20000-50000 hertz.
Step 4: Test as well as Apply
- After changing, conserve the modifications as well as test on fragment material to ensure the setting attains the intended outcome.
Conclusion:
This versatility in frequency environments opens a selection of innovative possibilities, enabling specific personalization of texture, deepness, and detail in laser device inscription tasks. Also, the ability to fine-tune these specifications assists the exploration of sophisticated uses in industrial and creative contexts, highlighting the significance of regularity modulation as a key consider laser device material processing.